Imaginez un entrepôt fonctionnant avec une précision métronomique, une vitesse époustouflante et une rentabilité accrue. Autrefois considérés comme le privilège des grandes entreprises, les systèmes de stockage et de récupération automatisés (AS/RS) font désormais leur entrée en force dans les petites et moyennes opérations. Grâce aux avancées technologiques, ces systèmes high-tech offrent aujourd’hui une gamme impressionnante d’options pour répondre aux besoins de tous les secteurs et budgets.
Plus qu’une simple tendance, l’adoption des systèmes AS/RS est en plein essor, transformant radicalement la manière dont les entreprises gèrent leurs stocks et expédient leurs commandes. Vous vous demandez si ces innovations sont faites pour vous ? Dans notre article, nous vous proposons un tour d’horizon des systèmes AS/RS, de leur définition à leurs multiples applications, en passant par les différents types et coûts associés.
Ne manquez pas cette occasion d’optimiser votre logistique et de propulser votre entreprise vers de nouveaux sommets de performance !
Qu’est-ce qu’un système automatisé de stockage et de récupération (AS/RS) ?
Dans le monde effréné de la logistique et de la gestion des entrepôts, les systèmes de stockage et de récupération automatisés (AS/RS) se sont révélés être de véritables game-changers. Ces systèmes intelligents, qui combinent des équipements de manutention automatisés, des logiciels de gestion et des structures de stockage, révolutionnent la manière dont les entreprises stockent, localisent et expédient leurs produits.
AS/RS, c’est avant tout un moyen d’optimiser l’espace, le temps et la main-d’œuvre dans les entrepôts. En automatisant les processus de stockage et de récupération des articles, ces systèmes permettent d’éliminer les erreurs humaines, d’accroître la précision et la rapidité des opérations, tout en réduisant les coûts et les risques associés au travail manuel. Du fait de la variété de ses applications, la technologie AS/RS varie considérablement et peut consister en des navettes, des grues, des carrousels, des modules de levage vertical (VLM), des Micro-Loads, des Mini-Loads, des Unit-Loads voir encore d’autres systèmes. Il est souvent intégré à un logiciel d’exécution d’entrepôt (WES), un logiciel de gestion d’entrepôt (WMS) afin de coordonner les différentes activités logistiques avec ce système
En résumé, ces systèmes ingénieux fonctionnent grâce à une combinaison de convoyeurs, de navettes, de grues et de robots, qui sont guidés par des logiciels sophistiqués et des capteurs pour assurer un contrôle précis des mouvements et des emplacements des produits. Le tout est orchestré de manière à répondre aux exigences spécifiques de chaque entreprise, avec une adaptabilité et une flexibilité remarquables.
Disponibles en plusieurs types et tailles, les systèmes AS/RS s’adaptent à des environnements variés, des petites opérations aux gigantesques centres de distribution. Ainsi, quels que soient la taille de votre entreprise ou votre secteur d’activité, les systèmes AS/RS peuvent vous aider à franchir un cap en matière de gestion de vos stocks et de votre chaîne logistique.
Avantages de l’AS/RS
En automatisant la tâche de faible valeur et facilement répétée du stockage et de la récupération des stocks, l’AS/RS apporte de nombreux avantages puissants aux opérations qui l’utilisent, notamment :
- Utilisation plus efficace de l’espace au sol
- Possibilité de récupérer l’espace vertical inutilisé
- Augmentation de la densité de stockage des stocks
- Ergonomie et sécurité améliorées, d’où une diminution des accidents
- Augmentation du débit
- Réduction des coûts de main-d’œuvre
- Moins de contraintes liées à la pénurie de main-d’œuvre
- Conception souvent modulaire pour une flexibilité maximale
- Précision accrue de la préparation des commandes
- Sécurité accrue des produits pour les stocks de première qualité
Utilisations et applications d’AS/RS
1. Marchandises à la personne pour la préparation et l’emballage des commandes
La préparation, l’emballage et le traitement des commandes constituent l’une des tâches les plus chronophages du processus d’exécution des commandes. En fait, le processus de marche et de prélèvement manuel des commandes peut représenter plus de 50 pour cent du du temps associé à la préparation de commande. AS/RS offre une alternative à cela en utilisant la préparation de commandes de type Goods-to-Person (GTP, ou G2P).
Dans un système de préparation de commandes de type Goods-to-Person, le travailleur ne se déplace pas physiquement d’un emplacement de produit à un autre pour préparer une commande. Au lieu de cela, une grue AS/RS Mini-Load, une navette, un AMR, un carrousel ou un VLM est capable d’extraire le stock nécessaire de l’entrepôt et de le livrer directement au travailleur, qui opère dans une station de prélèvement/emballage. Une fois que la quantité appropriée de produits a été prélevée, le stock est renvoyé au magasin et l’article suivant nécessaire à la commande est livré au travailleur pour qu’il le prélève.
Cela peut se faire sur la base d’une caisse complète ou d’une caisse fractionnée, selon l’opération. Dans l’un ou l’autre de ces scénarios, le système AS/RS peut ordonner les produits de manière à ce qu’ils soient les plus logistiques possibles – en permettant aux caisses de produits lourds d’être placées au bas d’une palette, par exemple, ou en organisant les produits de manière à ce que les produits similaires soient ensemble ou en séquence pour correspondre à la disposition du magasin, à la zone d’expédition et à l’heure limite, pour ne citer que quelques options.
2. Mise en scène des commandes pour l’expédition
L’impact du commerce électronique et de la livraison omnicanale sur le processus d’exécution des commandes ne peut être surestimé. Les clients sont désormais en mesure de faire des achats et de passer des commandes 24 heures sur 24, et ils veulent que leur produit livrés rapidement et à temps. Mais même si une entreprise accepte et traite les commandes 24 heures sur 24 et 7 jours sur 7, les fenêtres d’expédition sont souvent soumises à des contraintes : En raison des équipes de travailleurs, par exemple, ou des frais exorbitants de livraison la nuit et le week-end.
Pour pallier ces contraintes, une opération peut préparer et traiter les commandes en continu et utiliser un AS/RS pour les placer dans un magasin tampon afin de les mettre en attente jusqu’à ce que la fenêtre d’expédition soit ouverte. Cela permet de gagner du temps et de produire en continu, même lorsque les commandes ne peuvent pas quitter physiquement l’établissement.
3. Gestion du stockage tampon
Dans un entrepôt typique, les différents processus prennent des temps différents pour être achevés. Si ces écarts ne sont pas correctement gérés, il suffit d’un équipement mal réglé ou d’un ralentissement de zone à n’importe quelle étape pour que l’ensemble d’une opération s’arrête ou subisse un ralentissement massif.
La mise en mémoire tampon vise à prévenir une telle panne en garantissant que suffisamment de fournitures/produits sont toujours disponibles dans les différentes étapes pour maintenir une opération en cours. Mais si la mise en tampon a du sens, mal gérée, elle peut devenir un cauchemar logistique, nécessitant des kilomètres de convoyeur pour mettre en tampon et étager correctement.
Le système AS/RS a le potentiel de remplacer ces systèmes de mise en tampon par convoyeur, permettant à une opération de stocker efficacement le produit tampon et de le récupérer si nécessaire. Selon les spécificités de l’opération, cette gestion tampon peut être mise en place dans plusieurs domaines du flux de travail d’une opération, qu’il s’agisse de la mise en place de produits/matières premières au moment de leur livraison (« tampon de réception entrant ») ou du stockage de l’inventaire exactement à l’endroit où il sera nécessaire le long de la ligne de production (« tampon de point d’utilisation de la ligne d’assemblage ») ou (consolidation des commandes) du stockage de plusieurs parties d’une commande prélevées dans différentes zones, puis de leur consolidation pour l’emballage final et l’expédition.
4. Stockage et stockage au point d’utilisation
L’un des principaux avantages de l’AS/RS est sa capacité à stocker les produits de manière à utiliser le plus efficacement possible l’espace disponible, surtout à long terme. En mettant en œuvre le système AS/RS, une entreprise peut automatiser son stockage à long terme de matières premières ou de produits et récupérer ce dont elle a besoin, quand elle en a besoin.
En intégrant le système AS/RS à son logiciel d’exécution d’entrepôt (WES), il est également possible d’utiliser intelligemment et d’optimiser l’inventaire via FIFO (First in First Out), LIFO (Last In First Out), les numéros de lot, les dates d’expiration, les heures limites de commande, les exigences d’emballage et de nombreuses exigences spécifiques à l’organisation et à l’industrie
Types de systèmes de stockage et de récupération automatisés (AS/RS)
Systèmes de stockage et de récupération automatisés (AS/RS) se déclinent en deux grandes variétés : AS/RS à chargement unitaire et AS/RS à chargement miniature. Entre ces deux grandes catégories, il existe six types principaux de systèmes AS/RS :
- Grues AS/RS à charge unitaire (allées fixes et allées mobiles)
- Grues AS/RS à mini-charge
- AS/RS à navette et à robot
- AS/RS à carrousel (verticaux, horizontaux et robotiques)
- Module de levage vertical (VLM) AS/RS
- Micro-charges (stockeur)
Nous explorons chacun d’entre eux plus en détail ci-dessous.
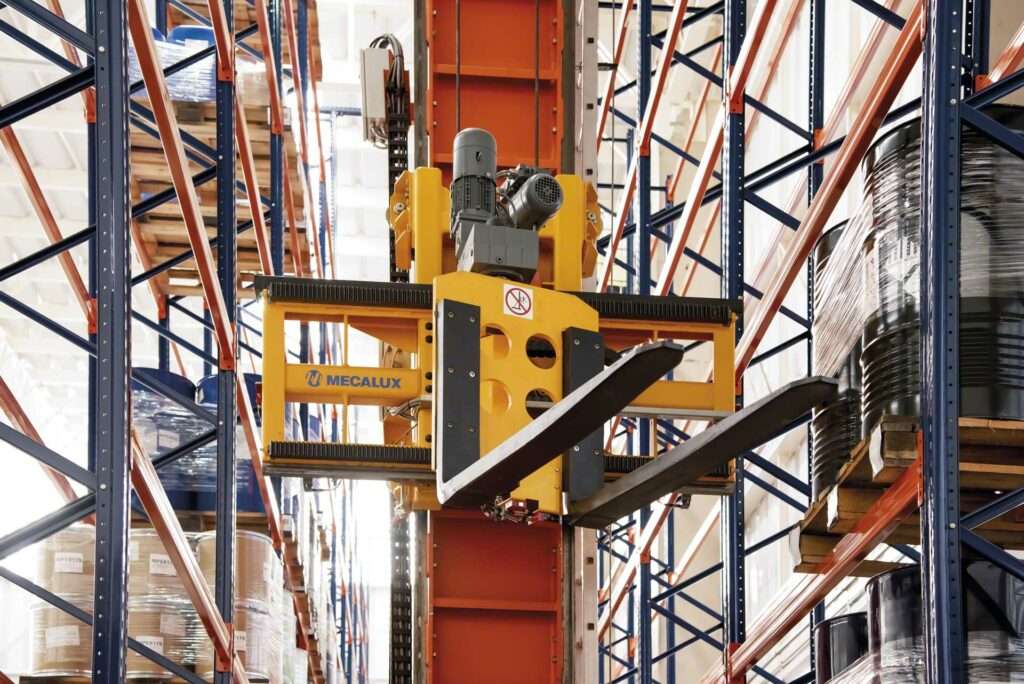
Systèmes AS/RS à charge unitaire
Les systèmes AS/RS à charge unitaire sont généralement utilisés pour manipuler des charges exceptionnellement grandes et lourdes allant de 1 000 à 5 500 Kilos. Cette capacité permet aux systèmes AS/RS à charge unitaire de manipuler des palettes et des caisses complètes ou partielles
Habituellement, le système AS/RS à chargement unitaire se compose de rayonnages à allées étroites, qui peuvent s’étendre à des hauteurs supérieures à 12 mètres et qui abritent des palettes de produits et de stocks. Ces rayonnages sont associés à une grue, qui est utilisée pour placer et récupérer physiquement les palettes selon les besoins
Le système AS/RS à chargement unitaire est une option particulièrement utile lorsque le stockage au niveau des palettes est limité et qu’une récupération rapide est essentielle
Les deux principales formes que prend le système AS/RS à chargement unitaire sont les grues à allées fixes et les grues à allées mobiles.
Grue à allées fixes AS/RS à chargement unitaire
Dans les systèmes Unit-Load AS/RS à allées fixes, les rayonnages à palettes sont disposés avec des allées étroites entre eux. Une grue se déplace entre ces allées, à la fois verticalement et horizontalement, pour récupérer et stocker les produits. La grue est fixée à une seule allée de palettes
Chargement unitaire en allées mobiles AS/RS Grue
Chargement unitaire en allées mobiles AS/RS fonctionne à peu près de la même manière que le système AS/RS à charge unitaire en allées fixes. Il s’agit d’une grue qui se déplace entre des allées étroites de palettes le long d’une sorte de rail. La différence essentielle est qu’elle n’est pas fixée à une allée spécifique. Cette capacité permet à une seule pièce d’équipement de desservir plusieurs allées et, en fin de compte, un plus grand espace de travail.
Mini-Load AS/RS
Mini-Load AS/RS traite généralement des charges plus petites (jusqu’à 15 Kg) par rapport aux systèmes à charge unitaire. Au lieu de palettes complètes, le Mini-Load AS/RS manipule des bacs, des plateaux et/ou des cartons. Ces systèmes sont parfois appelés systèmes de « manutention de caisses » ou « d’empilage de fourreaux ».
Le système AS/RS Mini-Load est particulièrement bien adapté aux opérations qui nécessitent des emplacements de stockage pour un grand nombre d’UGS, mais qui ne disposent pas de l’espace au sol requis par les rayonnages traditionnels à flux de cartons pour fournir une face de prélèvement pour chaque UGS. Les systèmes AS/RS à mini-charge peuvent également être utilisés pour mettre en mémoire tampon et libérer/séquencer efficacement les produits vers les stations de prélèvement ou de palettisation, et peuvent être utilisés pour réapprovisionner automatiquement les emplacements de prélèvement comme le flux de carton.
Système AS/RS à navette
Le système AS/RS à navette livre les stocks par le biais d’une navette ou d’un « robot » qui se déplace sur un rail entre une structure de rayonnage
Ils peuvent fonctionner sur un seul ou plusieurs niveaux, selon les besoins de l’opération, et peuvent être alimentés par des batteries ou des condensateurs. Les navettes livrent le fourre-tout ou le carton à un poste de travail intégré au système.
Lorsqu’un article est demandé, la navette se rend à l’emplacement du produit et récupère le fourre-tout ou le carton qui contient l’article demandé. La navette emmène ensuite le fourre-tout ou le carton directement à un poste de travail ou le transfère à un convoyeur pour transporter le fourre-tout ou le carton à un poste de travail.
Les différents modèles de navette utilisent des conceptions différentes pour offrir des avantages différents. Par exemple, un modèle est orienté verticalement pour optimiser l’espace au sol. Les navettes se déplacent sur le périmètre du rack, puis se déplacent dans une allée pour extraire un fourre-tout et le livrer à son poste de travail intégré.
Un troisième modèle de navette utilise un rack vertical, mais chaque robot se déplace sur le sol et grimpe verticalement pour extraire son tote. Il redescend ensuite au sol et livre indépendamment le stock à un poste de travail distant. Il fait la queue au poste de travail jusqu’à ce qu’il soit prélevé, puis on lui assigne automatiquement une nouvelle tâche et il répète le processus.
AS/RS haute densité basé sur AMR
Unsystème de stockage et de récupération automatisé haute densité basé sur des robots mobiles autonomes est conçu de manière à utiliser des robots AMR à trois axes pour se déplacer verticalement dans les rayonnages de stockage afin de récupérer le bac ou la caisse de stockage requis. L’AMR stocke le stock ou la caisse sur lui-même, puis descend le long du rack et sur le sol jusqu’à l’un des postes de travail de préparation de commandes à distance. L’AMR monte sur la rampe du poste de travail, et le système intégré de prélèvement et de logiciel indique l’article et le nombre à prélever. L’opérateur place ensuite l’article et la quantité appropriés dans l’une des commandes groupées et l’AMR part pour sa prochaine affectation.
Ce système offre une très grande souplesse en matière de densité de stockage, de débit et de besoins en main-d’œuvre. Des racks et des robots AMR supplémentaires peuvent être ajoutés, soustraits ou déplacés pour répondre aux niveaux d’activité actuels et prévus.
Système AS/RS basé sur un carrousel
Les systèmesAS/RS basés sur des carrousels sont constitués de bacs de produits ou de stocks qui tournent en continu le long d’un rail. Lorsque l’opérateur demande un article particulier, le système tourne automatiquement pour que le bac approprié soit accessible et que l’article puisse être prélevé. Un Lightree intégré indique au préparateur de commandes quel carrousel, quelle étagère et quel article il doit prélever.
Les AS/RS basés sur des carrousels peuvent consister en uncarrousel horizontal (les bacs se déplacent horizontalement, comme sur un manège) ou uncarrousel vertical (les bacs se déplacent verticalement, comme sur une grande roue). Les carrousels horizontaux sont souvent utilisés pour les petits articles et les pièces, ainsi que pour les documents ou les matières premières.
Lecarrousel horizontal robotisé AS/RS est une autre variété qui offre une fonctionnalité AS/RS entièrement automatisée
Dans ces systèmes, jusqu’à trois niveaux de carrousels sont empilés les uns sur les autres, et des bacs ou des caisses sont chargés sur chaque niveau d’étagère. Les trois carrousels verticaux fonctionnent indépendamment pour présenter l’inventaire nécessaire à un dispositif d’insertion/extraction qui se déplace horizontalement devant eux. Le dispositif d’insertion/extraction prend jusqu’à deux bacs ou cartons par voyage vers le convoyeur d’enlèvement, qui livre les marchandises à un poste de travail, et ramasse l’inventaire de retour, le replaçant dans une étagère d’attente. Il est possible d’augmenter la capacité et le débit en augmentant le nombre de rangées de carrousels précédées d’un inserteur/extracteur.
Module de levage vertical (VLM)
Un module de levage vertical (VLM) est un système fermé composé d’une inséreuse/extracteur au centre et d’une colonne de plateaux de chaque côté. Il s’agit d’une forme de technologie Goods-to-Person.
Lorsqu’un article est demandé, l’inséreur/extracteur localise le plateau nécessaire, le récupère et le remet à un opérateur, qui complète la commande. Une fois la commande terminée, le VLM remet le plateau à sa place avant de récupérer le prochain plateau demandé.
Les plateaux peuvent être fixes ou dynamiques. Dans les systèmes fixes, les plateaux individuels sont toujours renvoyés au même endroit ; dans un système dynamique, l’endroit où sont stockés les plateaux individuels varie.
Stockeur à micro-charges
Un stockeur Micro-Load permet le stockage et la récupération de bacs ou de cartons discrets ou individuels. Il est idéal pour le tamponnage, le séquençage et les articles de point d’utilisation dans un espace à haute densité
Le système est fermé et dispose d’un dispositif d’insertion/extraction qui fonctionne au centre du système, prélevant une file d’attente spécifique de stocks et les déchargeant ensuite sur un convoyeur ou un poste de travail en attente. Les différents modèles stockent et récupèrent différemment, en prenant soit un article, soit un groupe de cinq articles maximum en un seul passage
Ce système peut également être utilisé pour stocker des UGS jusqu’à ce qu’elles soient nécessaires, puis les décharger sur un convoyeur en attente. Il peut être intégré à d’autres systèmes AS/RS pour améliorer les performances des autres systèmes et réduire considérablement les besoins en convoyeurs et en espace au sol.
Synoptique des types d’AS/RS
Type d’AS/RS | Description | Avantages |
---|---|---|
Unit Load AS/RS | Système utilisant des grues automatisées pour déplacer des palettes ou des conteneurs entiers. | Gestion efficace des charges lourdes, gain de place |
Mini Load AS/RS | Système similaire à l’Unit Load AS/RS, mais conçu pour gérer des charges plus petites, telles que des bacs ou cartons. | Convient aux articles de petite taille, flexibilité |
Shuttle AS/RS | Système utilisant des navettes automatisées pour stocker et récupérer des palettes ou des conteneurs dans les allées. | Rapidité, haute densité de stockage, flexibilité |
AS/RS à rayonnages mobiles | Systèmes avec des rayonnages mobiles qui se déplacent pour créer un accès aux allées lorsque nécessaire. | Optimisation de l’espace, adaptabilité |
AS/RS pour picking | Système conçu pour améliorer le processus de picking en amenant les articles directement aux opérateurs. | Augmentation de la productivité, réduction des erreurs |
AS/RS vertical (VLM) | Système de stockage vertical avec des plateaux extractibles pour optimiser l’utilisation de l’espace en hauteur. | Gain de place, sécurité, ergonomie |
AS/RS robotisé (AMR) | Système utilisant des robots autonomes pour déplacer des articles dans l’entrepôt. | Flexibilité, scalabilité, réduction des coûts de main-d’œuvre |
Qu’est ce qui détermine le prix d’un AS/RS ?
Comme c’est le cas pour pratiquement toute technologie d’automatisation des entrepôts, le coût final d’un système automatisé de stockage et de récupération peut varier considérablement d’une opération à l’autre et même d’un secteur à l’autre. Le moyen le plus sûr d’avoir une idée claire de ce que coûtera la mise en œuvre d’un système AS/RS dans votre entreprise est de vous adresser à demander une consultation d’un intégrateur de systèmes compétent et digne de confiance
Ceci étant dit, en comprenant les différents facteurs qui influencent généralement le coût final de l’investissement, il est possible d’estimer où se situera votre nouveau système sur l’échelle des coûts. Voici lessept plus importants facteurs de coût du système AS/RS que vous devez prendre en compte :
- La hauteur libre disponible dans votre installation
- Le type d’environnement où il sera mis en œuvre (ambiant, réfrigéré, congélateur, salle blanche, etc.)
- La taille (cube) plus (et la qualité) de la charge à manipuler
- Le poids de chaque pièce
- Les systèmes d’entrée et de sortie en place pour acheminer les stocks vers et depuis le système
- Si l’installation a une structure en acier ou est soutenue par des crémaillères
- Les coûts de main-d’œuvre actuels et la quantité de main-d’œuvre
La technologie AS/RS convient-elle à votre entrepôt ?
La pertinence de la technologie AS/RS dans le cadre de vos activités dépendra largement des spécificités de votre entreprise. Des facteurs tels que votre cycle d’activité, vos objectifs opérationnels, votre niveau de croissance et le capital d’investissement disponible auront tous un impact sur votre capacité à mettre en œuvre un système. Il serait bon de parler à un consultant en conception d’entrepôt ou à un intégrateur de systèmes pour vous aider à déterminer si le système AS/RS a du sens pour vous.
Si vous répondez « Oui » à l’une des questions suivantes questions ci-dessoussi vous répondez « Oui » à l’une de ces questions, alors la mise en œuvre d’un système de stockage et de récupération automatisé pourrait être une décision judicieuse pour votre entreprise :
- Avez-vous besoin d’augmenter le débit de vos opérations ?
- Vos coûts de main-d’œuvre augmentent-ils ?
- Avez-vous des difficultés à embaucher pour les postes ouverts ?
- La rétention de travailleurs qualifiés est-elle un défi ?
- Manquez-vous d’espace dans vos installations ?
- Avez-vous besoin d’un meilleur contrôle des stocks ?
- Avez-vous des préoccupations ou des problèmes d’ergonomie des travailleurs ?
Et pour terminer la traditionnelle petite FAQ
Qu’est-ce qu’un système de stockage et de récupération automatisé (AS/RS) ?
Un système de stockage et de récupération automatisé (AS/RS) est un système de stockage automatisé qui utilise des machines pour stocker et récupérer des produits dans un entrepôt. Les AS/RS sont conçus pour maximiser l’utilisation de l’espace de stockage en minimisant l’espace perdu et en optimisant le temps de stockage et de récupération.
Comment fonctionne un système de stockage et de récupération automatisé (AS/RS) ?
Un système de stockage et de récupération automatisé (AS/RS) utilise des machines, telles que des chariots élévateurs automatisés ou des transtockeurs, pour stocker et récupérer les produits dans l’entrepôt. Les produits sont placés sur des palettes ou des conteneurs, puis transférés par la machine vers une zone de stockage. Les produits peuvent être récupérés de la même manière en utilisant les machines pour les récupérer et les déplacer vers la zone de récupération.
Quels sont les avantages d’un système de stockage et de récupération automatisé (AS/RS) ?
Les avantages d’un système de stockage et de récupération automatisé (AS/RS) sont nombreux. Ils comprennent une meilleure utilisation de l’espace de stockage, une réduction des erreurs de stockage et de récupération, une meilleure sécurité pour les travailleurs, une augmentation de la productivité et une réduction des coûts de main-d’œuvre.
Quels sont les types de systèmes de stockage et de récupération automatisés (AS/RS) ?
Il existe plusieurs types de systèmes de stockage et de récupération automatisés (AS/RS) qui peuvent être utilisés en fonction des besoins de l’entreprise. Les types courants comprennent les systèmes à allées étroites, les systèmes à navettes, les systèmes de stockage en bloc et les systèmes de stockage à tambour.
Quels sont les critères à prendre en compte lors du choix d’un système de stockage et de récupération automatisé (AS/RS) ?
Les critères à prendre en compte lors du choix d’un système de stockage et de récupération automatisé (AS/RS) dépendent des besoins de l’entreprise. Les critères courants comprennent la hauteur de stockage, le débit de stockage et de récupération, le coût du système et la flexibilité du système pour répondre aux besoins futurs de l’entreprise.